Learning
Through many cycles of learning and continuous improvement, Develop Consulting truly believes that although complimentary, Lean and Six Sigma methodologies have differing outputs and focus.
Lean is typically a cultural engagement and a transformational approach while Six Sigma is very much a sophisticated analytical tool.
But the questions remain:
Do you understand the problems facing your business today?
Do you know why you need a Lean or Six Sigma strategy in your business?
Do you realize the benefits of implementing Lean or Six Sigma methodologies?
Our purpose is to help you find the right Lean Six Sigma training class that will deliver the biggest impact for you and your organization.
Our Lean Six Sigma Training Classes & Workshops
Inspired by the Japanese management methods and more specifically, the Toyota Production System, the Lean approach is intended to have the enterprise think first and foremost about maximizing the value that its service can bring to the customer.
Lean White Belt - 1 Day
This class aims to put all attendees on the first step towards a Lean transformation.
Lean Yellow Belt – 2 Day
This class provides participants with an overview of the basic principles of Lean Thinking and outlines the essential Lean tools and practices.
Lean Green Belt – 5 Day
This class provides participants with an understanding of the theory and effective application of Lean concepts, tools and practices within their environment.
Lean Six-Sigma Black Belt – 5 Day (Green Belt Prerequisite)
This program provides a complete understanding of the Lean Six Sigma DMAIC framework.
Lean Six Sigma Executive Training
For those seeking a clear understanding of the role they play in the Lean implementation process and greater understanding of the leadership and practical skills required to influence, inspire and motivate others to excel.
Duration – 1 or 3 Days
This class will provide Executives with practical tools to understand what their role is in supporting any transformational change program and what is required to sustain change.
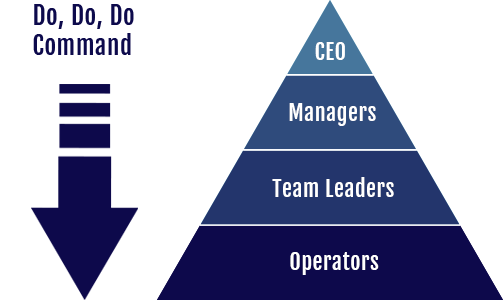
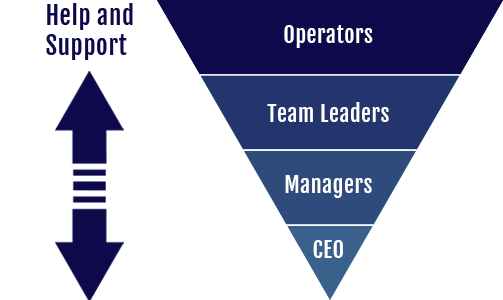
Before Lean
- Directive and hierarchical
- Information only flows downwards
- Often lack of support for operators
- Lack of trust and coercion environment
After Lean
- Supportive and communicative
- Information flows both ways
- Operators regarded as experts
- Support, trust and co-operation
Lean Coaching & Support:
Our coaching and support primarily focuses on looking for solutions rather than looking back to the past. We believe our skill is to reframe the story to be solvable. We use an integrated goal focused model that encourages collaboration between the individual and the coach.
Duration
Flexible
Method
Face to face or remote support
Rapid Improvement Events
Duration – 2 to 5 days
Rapid Improvement Events (RIE) are about taking the existing baseline and improving it. It starts with walking the entire process, we call it “going to Gemba”, which is Japanese for going to see how the work is done. You would be surprised when a group of people comes together to describe how a process works, and they all have different perspectives on the same process.
The RIE takes place in your chosen area with key members of staff plus a few additional people from supporting areas, and management.